Thursday, November 21, 2024
Reclaim Your Space: Building a Lean-To Shed the Easy Way

Reclaim Your Space: Building a Lean-To Shed the Easy Way
The desire for additional storage or workspace is a common challenge faced by homeowners. While constructing a fully enclosed shed can be a significant undertaking, a lean-to shed presents a more manageable and efficient solution. This guide provides a comprehensive overview of building a lean-to shed, emphasizing simplicity and practicality for the DIY enthusiast.
Planning and Design Considerations
Before commencing construction, meticulous planning is crucial to ensure a successful outcome. This phase involves several key steps, each contributing to the overall structural integrity and functionality of your lean-to shed.
Determining the Location and Size
The optimal location for your lean-to shed depends on several factors. Consider proximity to existing structures, access to utilities (if required), and the prevailing wind direction. Assess the available space and determine the desired dimensions of your shed. Remember to check local building codes and regulations before proceeding. Overly ambitious dimensions for a first-time builder are strongly discouraged; a smaller, simpler structure is a more achievable and less frustrating project.
Choosing the Right Materials
Material selection significantly impacts the durability, cost, and aesthetic appeal of your lean-to shed. Pressure-treated lumber is highly recommended for its resistance to rot and insect damage, especially for the foundation and framing. Consider using composite materials for decking or siding for low-maintenance appeal. For roofing, asphalt shingles are a popular and cost-effective choice, offering good protection against the elements. Explore different roofing options to find one that aligns with your budget and aesthetic preferences.
Consider these factors when choosing your materials:
- Budget: Establish a realistic budget and select materials accordingly. Pricing varies significantly between lumber grades and composite materials.
- Durability: Prioritize materials known for their resistance to weather damage, pests, and decay.
- Aesthetics: Choose materials that complement the existing structures on your property.
Obtaining Necessary Permits
Depending on your location and the size and complexity of your lean-to shed, you may be required to obtain building permits. Contact your local building department to inquire about permit requirements and submit the necessary applications well in advance of construction. Failure to obtain necessary permits can result in fines or even demolition orders.
Foundation and Framing
A solid foundation is paramount for a stable and long-lasting lean-to shed. The framing provides the structure's skeleton, supporting the roofing and walls. Careful execution of these steps is crucial for the overall success of the project.
Preparing the Foundation
A simple concrete slab or a compacted gravel base provides a suitable foundation for a lean-to shed. For a concrete slab, ensure the ground is level and properly compacted. For a gravel base, excavate to a suitable depth, add gravel, and compact thoroughly. The foundation's dimensions should match or slightly exceed the planned footprint of the shed.
Constructing the Frame
The frame of your lean-to shed will typically consist of pressure-treated lumber. Begin by constructing the base frame, ensuring squareness and levelness. Erect the vertical supports, ensuring they are plumb and properly braced. Install the roof rafters, ensuring they are properly spaced and securely attached to the vertical supports and the supporting wall of the existing structure. Use appropriate fasteners, such as galvanized nails or screws, to ensure strong connections.
Accuracy is paramount during framing. Use a level and square to ensure all components are properly aligned. Improper framing can compromise the structural integrity of the shed.
Roofing and Siding
Once the framing is complete, you can proceed with roofing and siding installation. These steps contribute to the shed's weather resistance and aesthetic appeal.
Installing the Roofing
The roofing process begins with installing underlayment, a waterproof membrane that protects the structure from moisture. Then, install your chosen roofing material, following the manufacturer's instructions carefully. Ensure proper overlapping of shingles or other roofing materials to prevent leaks. Secure all roofing materials with appropriate fasteners.
Proper ventilation is important to prevent moisture buildup. Consider installing ridge vents or other ventilation features.
Adding Siding
Siding protects the structure's interior from the elements and enhances its appearance. Choose your siding material and install it according to the manufacturer's instructions. Ensure proper alignment and overlapping of siding pieces. Seal any gaps or seams to prevent water infiltration.
Finishing Touches and Considerations
Once the primary construction is complete, several finishing touches can improve the functionality and aesthetics of your lean-to shed.
Adding a Door or Window
A door provides convenient access to the shed's interior. A window allows for natural light and ventilation. Select and install appropriate doors and windows, ensuring they are properly sealed to prevent drafts and leaks.
Interior Finishing
Interior finishing can include painting or staining the walls and floor, adding shelving, and installing lighting. These additions improve the shed's usability and aesthetic appeal.
Safety Precautions
Throughout the construction process, prioritize safety. Wear appropriate personal protective equipment (PPE), including safety glasses, gloves, and hearing protection. Use caution when working with power tools and follow all manufacturer instructions. Ensure the work area is well-lit and free of obstructions.
Building a lean-to shed can be a rewarding and relatively straightforward project. By following these guidelines and exercising careful planning and execution, you can successfully create a valuable addition to your property, reclaiming valuable space and enhancing its functionality. Remember to always prioritize safety and adhere to local building codes and regulations throughout the construction process.
Build a Custom Pallet Shed with These Easy-to-Follow Plans
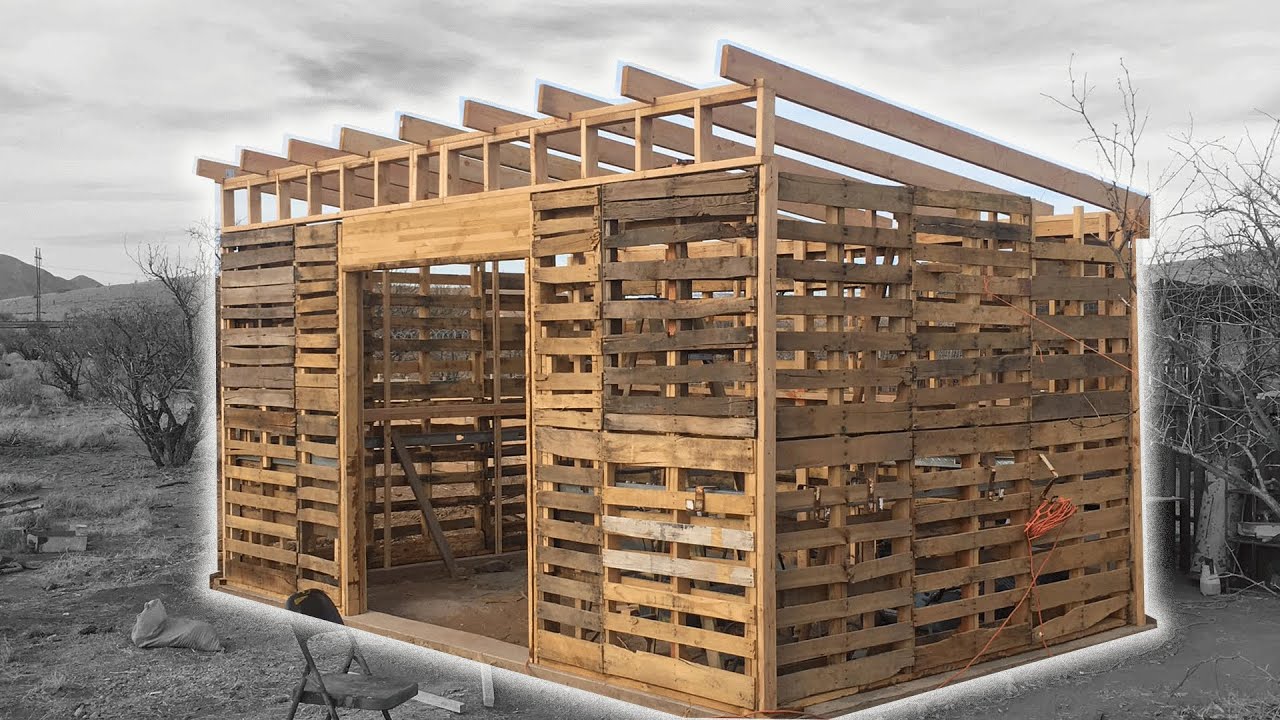
Build Your Own Custom Pallet Shed: A Step-by-Step Guide
Hey there, folks! So you're thinking about building a shed, huh? That's awesome! And even better, you're thinking about doing it with reclaimed pallets â" super eco-friendly and often budget-friendly too! This guide will walk you through building your very own custom pallet shed. Don't worry, it's not as daunting as it sounds. We'll break it down into manageable steps, and even if you're a total newbie to DIY, you can totally pull this off. Let's get started!Planning and Preparation: The Foundation of a Great Shed
Before you even think about touching a single pallet, some planning is essential. This stage will save you headaches (and maybe some materials) down the line.Choosing Your Palettes
This is crucial. Not all pallets are created equal! You need to source sturdy pallets that are in good condition. Look for pallets made of heat-treated wood (HT) â" you'll find this stamped on them â" as it's safer and less likely to have pests or harmful chemicals. Avoid pallets that are heavily damaged, rotting, or show signs of significant insect infestation. Consider the size and number of pallets you'll need based on your desired shed dimensions. Visiting local businesses (like grocery stores or lumber yards) and asking if they have any to spare is a great way to get free or cheap pallets.Designing Your Shed: Size and Style
Sketch out a basic design. How big do you want your shed? How much stuff do you need to store? Think about the door placement, roof style (a simple gable roof is easiest for beginners), and any windows you might want. A simple rectangular shed is the easiest to construct. Remember, this is a pallet shed, so keep the design relatively straightforward. Don't overthink it â" simple is often best!Gathering Your Tools and Materials
Beyond pallets, you'll need a few things:- Measuring tape
- Level
- Hammer or nail gun (a nail gun is a huge time saver!)
- Screws (long, heavy-duty exterior screws are recommended)
- Wood glue (exterior grade)
- Safety glasses
- Work gloves
- Saw (circular saw or hand saw)
- Post hole digger (if you're creating a more permanent foundation)
- Concrete (optional, for a more permanent foundation)
- Roofing felt or other roofing material
Building the Frame: The Shed's Skeleton
Now for the fun part! We'll start by constructing the frame of your shed.Creating the Base
Lay down your chosen base â" either directly on the ground, on compacted gravel, or even on a small concrete slab for a more permanent structure. Arrange your pallets to form the desired base dimensions. Ensure they are level and secure. You can use screws or longer nails to fasten the pallets together.Building the Walls
This is where youâll use the remaining pallets to construct the walls. Remember to measure carefully before attaching the pallets. You might need to cut some pallets to fit perfectly. Use a combination of screws and wood glue for added strength. For a more structurally sound shed, consider adding vertical support beams (2x4s or similar) between the pallets to brace the walls.Constructing the Roof
For a gable roof, you'll create two triangular sections. Use more pallets (possibly cut to size) to form the roof rafters, making sure they are securely attached to the top of the walls. Then, cover your roof with roofing felt and your chosen roofing material. Shingles, corrugated metal, or even heavy-duty plastic sheeting can work.Finishing Touches: Making Your Shed Shine
Once the main structure is complete, it's time to add the finishing touches.Adding a Door
You can either use a pre-made door or create one using more pallets. If making your own, ensure it's properly reinforced and securely hung. Consider adding hinges and a latch for security.Adding Windows (Optional)
If youâd like windows, you can cut openings in your pallet walls and install some small windows. You can get inexpensive windows from a hardware store or even repurpose existing windows.Sealing and Painting (Optional)
To protect your shed from the elements and enhance its appearance, consider applying a sealant or weatherproofing treatment. You can also paint your shed to match your existing aesthetic.Safety First!
Remember safety first! Always wear safety glasses and gloves when working with tools and materials. Be mindful of lifting heavy pallets â" get help if needed. If you're unsure about any step, don't hesitate to consult with a more experienced DIY enthusiast or professional.
Commonly Asked Questions
Q: How long does it take to build a pallet shed?
A: This depends on the size and complexity of your shed, your DIY skills, and how many people are helping. A simple shed can take a weekend, while a more complex one might take several days or even longer.
Q: How much does it cost to build a pallet shed?
A: The primary cost is the materials beyond the pallets themselves. If you find free pallets, your cost could be surprisingly low. Otherwise, expect to spend between $100 and $500 on additional materials, depending on size and complexity.
Q: Are pallet sheds durable?
A: With proper construction and sealing, a pallet shed can be surprisingly durable. However, it's not as weather-resistant as a shed made from treated lumber. Regular maintenance is recommended.
Q: What kind of permits do I need?
A: Permitting requirements vary by location. Check with your local authorities before starting construction to ensure you comply with all regulations.
Q: Can I use any type of pallet?
A: No, use only heat-treated (HT) pallets. Other pallets may contain harmful chemicals or pests.
And there you have it! Building a pallet shed is a rewarding project that combines creativity, resourcefulness, and a whole lot of satisfaction. Remember to take your time, plan well, and enjoy the process! Happy building!Wednesday, November 20, 2024
DIY Lean-To Shed Build: Tips for Efficient and Affordable Construction
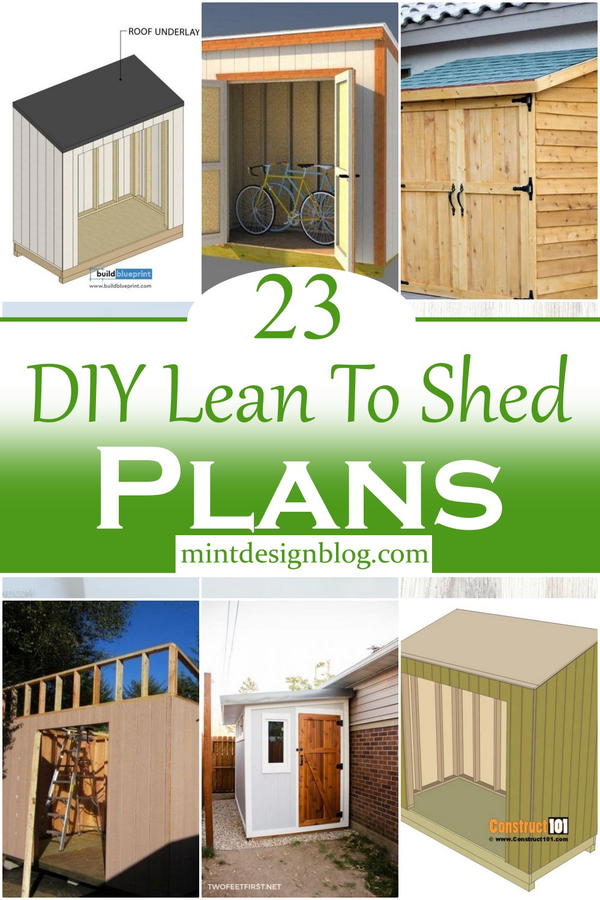
DIY Lean-To Shed Build: Tips for Efficient and Affordable Construction
Building your own lean-to shed offers a rewarding blend of practicality and cost savings. This simple structure provides valuable storage space while allowing you to hone your DIY skills. This guide provides a step-by-step approach to constructing an efficient and affordable lean-to, minimizing waste and maximizing your budget.
Planning Your Lean-To Shed
Before you even touch a tool, meticulous planning prevents costly mistakes down the line. Start by determining your shed's purpose. Will it house gardening equipment, bicycles, or simply overflow storage? This dictates the required size. Consider local building codes and regulations â" you might need permits depending on size and location. Sketch your design, noting precise dimensions for the roof, walls, and base. Accurate measurements are crucial for material purchasing and efficient construction.
Choosing the Right Location
Select a level, stable area for your lean-to. Consider proximity to power sources if you plan on adding electricity. Ensure the location allows for easy access and doesn't obstruct walkways or other structures. Proper drainage is also key; avoid low-lying areas prone to water accumulation.
Material Selection: Balancing Cost and Quality
Prioritize durability and affordability when choosing materials. Pressure-treated lumber resists rot and insects, making it an excellent choice for the base and framing. For the roofing, consider inexpensive yet durable options like corrugated metal or asphalt shingles. Source materials from local suppliers to minimize transportation costs. Compare prices from different suppliers to find the best deals.
Construction: A Step-by-Step Guide
With your plan finalized and materials gathered, construction begins. Start by preparing the base. Level the ground and create a foundation using concrete blocks, gravel, or a simple wooden base, depending on your chosen method and budget. This provides stability and prevents rot. Next, erect the frame, ensuring all angles are square and plumb. Use appropriate fasteners like screws or nails, reinforcing critical joints with metal brackets.
Framing and Roofing
The frame forms the skeleton of your shed. Construct the walls using the chosen lumber, ensuring they're firmly attached to the base. For the roof, install rafters, ensuring adequate slope for water runoff. Sheathe the roof with plywood or OSB board before applying your chosen roofing material. Remember to secure all elements to withstand weather conditions. Carefully follow the manufacturer's instructions for installing roofing materials.
Finishing Touches
Once the roof is complete, add any desired finishing touches. Consider adding a door for easy access. If you desire, paint or stain the exterior to protect the wood and enhance aesthetics. Installing simple shelving can dramatically improve storage organization. Consider adding ventilation to prevent moisture build-up.
Tips for Efficiency and Cost Savings
Maximize efficiency by organizing your tools and materials beforehand. Having everything readily available minimizes wasted time. Consider using recycled or reclaimed materials where possible, such as salvaged lumber for framing. Enlist help from friends or family to accelerate the construction process. Proper planning and execution minimizes material waste, contributing significantly to cost savings. Don't hesitate to seek guidance from experienced DIYers or watch helpful online tutorials.
Building a lean-to shed is a rewarding project that combines practicality and cost-effectiveness. By following these tips and paying close attention to detail, you can construct a durable, affordable structure that enhances your property and provides valuable storage space for years to come.
Saturday, November 16, 2024
12x20 Shed Loft Plans: Perfect for Hobbyists and Gardeners

12x20 Shed Loft Plans: Perfect for Hobbyists and Gardeners
So, you're dreaming of a bigger, better shed? One that's not just for storing gardening tools and lawnmowers, but a real workspace, a haven for your hobbies, maybe even a little quiet retreat? A 12x20 shed with a loft is the answer! It offers a surprisingly spacious footprint, and that added loft space unlocks a whole new world of possibilities. Let's dive into why a 12x20 shed with a loft is a fantastic investment and how you can make your dreams a reality.
Why Choose a 12x20 Shed with a Loft?
A 12x20 shed isn't just a bigger box; it's a versatile space waiting to be customized. The extra square footage is amazing, but the loft really takes it to the next level. Think about it: you get double the storage, double the potential!
Ample Storage: The Obvious Advantage
Let's face it, we all accumulate stuff. Garden tools, potting supplies, holiday decorations, sports equipment â" the list goes on and on. A 12x20 shed gives you the room to organize it all, and the loft allows for even more storage. Imagine neatly stacking away seasonal items, keeping your frequently used tools easily accessible downstairs, and having a dedicated space for everything else.
Dedicated Hobby Space: Unleash Your Creativity
Got a passion for woodworking, painting, sewing, or something else entirely? That 12x20 shed with a loft can become your dedicated creative sanctuary. The loft can serve as a studio, a workshop, or a quiet space to concentrate on your projects. No more cramming your hobbies into a cluttered corner of the garage!
Guest Room or Retreat: Unexpected Versatility
While not a full-fledged guest house, a well-insulated and finished 12x20 shed with a loft can make a surprisingly comfortable guest room for overnight visitors. Or, even better, it could be your personal escape â" a quiet reading nook, a meditation space, or a place to simply unwind and relax.
Planning Your 12x20 Shed Loft: Key Considerations
Before you grab your hammer and nails (or your blueprints and software!), there are a few crucial points to consider.
Local Building Codes and Permits: Do Your Homework
This is paramount. Contact your local building department to check on regulations for shed construction, including size limitations, foundation requirements, and necessary permits. Failing to obtain the proper permits can lead to hefty fines and even demolition orders. Believe me, it's worth the time and effort to get it right from the start.
Foundation: Stability is Key
Your shedâs foundation is crucial for long-term stability. Consider options like a concrete slab, concrete piers, or a pressure-treated lumber base. The choice will depend on your budget, soil conditions, and local building codes. A sturdy foundation will prevent settling and protect your investment.
Loft Access: Safety and Convenience
Think carefully about how youâll access the loft. A sturdy staircase is ideal, but a pull-down ladder can be a space-saving alternative. Consider the height of the loft ceiling and ensure the access point is safe and convenient.
Insulation and Climate Control: Year-Round Use
If you plan to use the shed year-round, proper insulation is a must. This will keep the interior comfortable, regardless of the weather. Consider adding insulation to the walls, roof, and floor. You might even think about adding a small heater or air conditioner, depending on your needs.
Designing Your Dream Space: Maximizing Functionality
This is where the fun really begins! Think about how you'll use your 12x20 shed and design the space accordingly.
Workbenches and Storage Solutions: Optimize Your Workspace
If you're using the shed as a workshop, invest in sturdy workbenches and plenty of storage solutions. Think about built-in shelving, cabinets, and pegboards to keep everything organized and accessible.
Electrical Wiring and Lighting: Powering Up Your Shed
Adding electricity is a great way to enhance the functionality of your shed. You'll need to hire a qualified electrician to ensure it's done safely and correctly. Proper lighting is essential for comfortable working conditions.
Ventilation: Maintaining a Healthy Environment
Proper ventilation is important, especially if you're using the shed for activities that generate dust or fumes. Install windows and vents to ensure good airflow and prevent the buildup of moisture.
Finishing Touches: Personalizing Your Space
Once the structure is complete, you can personalize your shed with paint, flooring, and other finishing touches. Choose materials that are durable and easy to maintain.
Building Your Shed: DIY or Professional?
The decision to build your shed yourself or hire a professional is a personal one. Building it yourself can be a rewarding experience, but it requires time, skills, and tools. Hiring a professional will save you time and effort, but it will come at a higher cost. Weigh the pros and cons carefully before making your decision.
Frequently Asked Questions
Here are some common questions people have about 12x20 shed loft plans:
Q: How much does a 12x20 shed with a loft cost?
A: The cost varies widely depending on materials, finishes, and whether you build it yourself or hire a contractor. You can expect to spend anywhere from a few thousand dollars to well over $10,000.
Q: Do I need a permit to build a 12x20 shed?
A: Yes, almost certainly. Check with your local building department. Permit requirements vary by location.
Q: How much space will I have in the loft?
A: The usable loft space will depend on the height of the ceiling and the design of the loft itself. You'll likely have several hundred square feet of additional storage or work space.
Q: What kind of materials should I use?
A: The best materials are durable, weather-resistant, and meet local building codes. Pressure-treated lumber for the frame, metal roofing for durability, and exterior-grade plywood or siding for the walls are good starting points.
Q: Can I add electricity to my shed?
A: Yes, but you must hire a qualified electrician to ensure it's done safely and to code. Improper electrical work is dangerous.
Building a 12x20 shed with a loft is a big undertaking, but the rewards are immense. With careful planning, thoughtful design, and a little elbow grease (or a skilled contractor!), you can create a versatile and functional space that enhances your lifestyle for years to come. So, start dreaming, start planning, and get ready to build your dream shed!
Monday, November 11, 2024
How to Make a Pole Barn with a High-Security Design
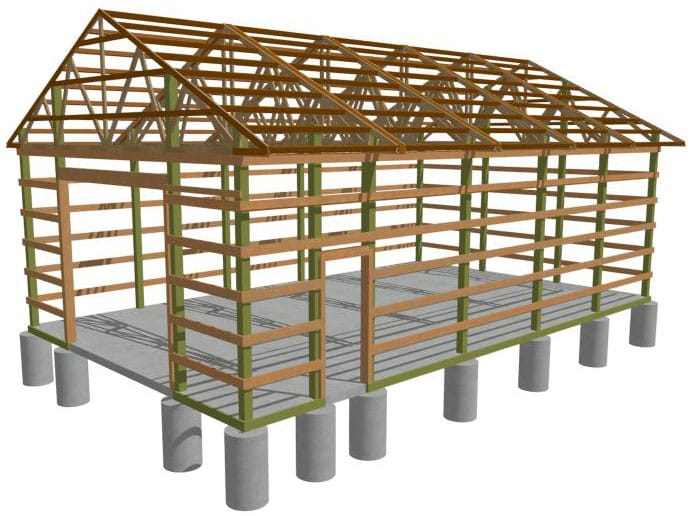
Alright, so you want to build a pole barn, but not just any old pole barn. You want a fortress, a security vault disguised as a barn. I get it, you want to keep your valuables safe and sound, and you want to make sure that no one, and I mean no one, gets in without your permission. Let's talk about how to make your pole barn a high-security masterpiece.
Start with the Foundation: A Solid Base for Security
First things first, let's get that foundation right. A strong foundation is like the bedrock of your security. Don't skimp on this part. Forget those standard concrete piers, we're talking about something serious.
Reinforced Concrete: Imagine those piers, but beefed up with rebar. Think of it as adding extra muscle to your foundation.
Deep Foundations: Instead of just a few feet down, go deeper. You want your foundation to be anchored firmly, like a ship riding out a storm.
Perimeter Security: Think about burying a security fence around the perimeter of your foundation. This adds another layer of protection right from the ground up.
The Poles: More Than Just Support
The poles are the backbone of your pole barn, so you want them to be strong and durable. We're not talking about your average lumberyard poles here. We're talking about a higher level of strength.
Heavy Duty Steel: Forget wood. You need steel poles that can withstand the weight of a bear, not just a few bags of hay.
Thick Gauge Steel: The thicker the gauge, the tougher the pole. You want a pole that can stand up to any pressure.
Corrosion Resistant Coating: You want these poles to last, so choose a steel that's protected against rust and corrosion.
Walls: A Fortress of Protection
Now let's talk about the walls. You want them to be more than just sheet metal. You want them to be the ultimate deterrent.
Thick Gauge Metal Siding: Again, we're talking about serious metal here, not some flimsy stuff. Think of the metal used in bank vaults.
Double-Walled Construction: Two layers of metal are better than one. It makes it much harder for someone to break in.
Impact Resistant Panels: Imagine a wall that can withstand the force of a battering ram. That's what we're aiming for here.
Reinforced Door Frames: Don't forget the doorways! They need to be just as strong as the rest of the walls. Consider steel door frames with additional reinforcement.
The Roof: A Shield Against the Elements
The roof isn't just about keeping the rain out. It's another line of defense.
Heavy Duty Metal Roofing: You want a roof that can withstand high winds and even hailstorms.
Reinforced Ridge and Eaves: These are the weak points of a roof, so they need to be strong and secure. Consider using metal bracing or heavy-duty corner brackets.
Security Roof Hatch: You might need access to the roof for repairs or inspections, but you want to control that access. A security hatch, with a lock, is a good idea.
Doors: The Gatekeepers to Your Fortress
The doors are the entry point, so they need to be rock solid. Don't skimp on these.
Security Doors: Forget those standard barn doors. We're talking about heavy-duty steel doors with multiple locks and reinforced hinges.
Electronic Locks: Add electronic locks that require a code or a fingerprint scan for entry. Consider a keypad lock for easy access.
Video Surveillance: Cameras on the doors can deter would-be thieves and provide evidence in case of a break-in.
Lighting and Alarms: The Eyes and Ears of Your Barn
You want to deter potential thieves and give yourself peace of mind, so invest in a good security system.
Motion Sensor Lighting: Floodlights activated by motion can scare off intruders and provide a clear view of the area.
Perimeter Alarms: Sensors around the perimeter can alert you to any trespassers.
Interior Alarms: Motion sensors, door alarms, and window alarms can alert you to any activity inside your barn.
Remote Monitoring: Consider a system that allows you to monitor your barn remotely from your phone or computer.
Beyond the Basics: Additional Security Measures
You've got the foundation, the walls, the roof, the doors, and the security system. But you can take it a step further.
Concealed Security Cameras: These cameras can be hidden in plain sight, making it harder for intruders to spot them.
Security Lighting: Install floodlights around the perimeter of your property that illuminate the area in case of intrusion.
Motion-Activated Sprinkler System: A well-placed sprinkler system can be a big deterrent to unwanted visitors.
Fencing: A secure fence around the perimeter of your property can prevent unauthorized access and deter potential thieves.
Dogs: A dog can be a valuable addition to your security system. Choose a breed that is known for its protective instincts.
The Last Line of Defense: Planning and Vigilance
Even with a high-security pole barn, it's important to remember that no system is perfect.
Security Audits: Regularly review your security system to make sure it's up to date and functioning properly.
Neighbors and Security Teams: Establish relationships with your neighbors and let them know about your security measures.
Stay Vigilant: Be aware of your surroundings and trust your instincts. Report any suspicious activity to the authorities.
Building a high-security pole barn takes time and effort, but it's an investment worth making. Remember, you want your barn to be a safe haven for your belongings and a symbol of your peace of mind.
DIY Guide to Building a Pole Barn with Custom Doors and Windows

Okay, you've got the land, the vision, and the itch to build. A pole barn, huh? Solid choice. You're in for a rewarding project, and let me tell you, there's nothing quite like the satisfaction of building something with your own two hands (and maybe a few power tools). We're going to dive deep into building your pole barn, but with a twist â" we're going to add some custom flair with unique doors and windows.
Getting Started: Blueprint and Materials
First things first, we need a solid plan. Grab a pen and paper (or fire up your favorite design software) and start sketching out your pole barn's dimensions. Consider the purpose, size, and features you want. Got a workshop in mind? Need storage space for your truck? Think about the layout and how you'll use the space.
Once you've got a good blueprint, it's time to get your materials list in order. Here's a breakdown of the key players:
Posts: Think sturdy, long-lasting, and pressure-treated to resist rot. Your trusty lumberyard will have plenty of options â" choose the size based on the load your barn will carry.
Skids/Footings: A solid base is crucial for stability. Concrete footings offer a permanent solution, while skids provide a more flexible setup. Decide what works best for your location and project needs.
Framing Lumber: This is the backbone of your walls and roof. Choose sturdy 2x4s or 2x6s for reliable strength.
Roofing: Go for a sturdy, weather-resistant material â" metal roofing is a popular choice for its durability and low maintenance. Don't forget about insulation!
Siding: Choose a style that complements your vision â" from classic wood to modern metal, the possibilities are endless!
Doors and Windows: This is where the custom fun begins! We'll talk more about this later.
Setting the Stage: Foundations and Posts
Alright, time to get your hands dirty! First, we need to set those sturdy posts in place. If you opted for concrete footings, dig holes according to your blueprint and pour the concrete. Allow plenty of time for the concrete to cure before moving on. If you're going with skids, ensure they're level and secure for a solid foundation.
Now, it's time to erect those posts. Use a level to make sure everything is plumb and straight. You might need a couple of helping hands for this step. Once they're firmly set, brace them for extra support.
Building the Walls: Framework and Sheathing
With the posts standing tall, we can start framing the walls. Attach your chosen framing lumber to the posts, making sure to measure carefully and ensure the walls are square. Remember, a well-constructed frame is key to a strong and durable barn.
Now, let's add some sheathing to the walls. This layer of plywood or OSB (oriented strand board) adds rigidity and creates a smooth surface for the siding. Use nails or screws to secure the sheathing to the framing, ensuring it's flush and even.
Roofing the Beast: Truss, Sheathing, and Cover
Time to put a roof over your head (or your barn, rather). For most pole barns, pre-engineered trusses provide a simple and strong solution. Follow the manufacturer's instructions for installation, ensuring they're properly spaced and secured to the posts.
Once the trusses are up, add sheathing to the roof just like you did with the walls. Now it's time for the roofing material â" choose your favorite and get to work! Remember, proper installation is key, so consult manufacturer instructions and maybe even call in a roofing pro if you're feeling unsure.
The Grand Finale: Siding and Finishing Touches
With the roof on, it's time to give your barn its personality. This is where you'll bring your siding vision to life. Whether it's classic wood, sleek metal, or a mix of both, choose your materials and follow the manufacturer's installation instructions.
Custom Doors and Windows: Your Personal Touch
Now, for the highlight â" the custom doors and windows! Here's where your creativity can truly shine.
Doors: Imagine a massive sliding door that welcomes you to your workshop, or a pair of rustic barn doors adding charm to your storage space. Think about how you'll access the barn and what kind of style complements your overall design.
Windows: Let in the natural light with custom windows. Consider placement for optimal sunlight in your workshop or to showcase your stunning views. Maybe even add some stained-glass accents for a touch of artistry!
Don't Forget the Details:
Hardware: Strong hinges, sturdy handles, and stylish door hardware will add functionality and character to your barn.
Paint and Stain: Add a splash of color or a natural wood finish to complete the look. Choose colors and finishes that complement your overall design and reflect your personal style.
Building Your Dream: One Step at a Time
Building a pole barn with custom doors and windows is a fulfilling journey. It takes time, effort, and a little bit of know-how. But don't be intimidated â" with proper planning, careful execution, and maybe a helping hand from a friend, you can achieve your vision and build the pole barn of your dreams.
Ready to Get Started?
I hope this guide has inspired you to embark on your own pole barn project. Remember, this is just a starting point â" research, plan, and personalize to create a space that reflects your unique needs and style. Have fun building!
DIY Pole Barn Plans: How to Plan for Multiple Use Purposes

So you're thinking about building a pole barn. Good for you! They're incredibly versatile, affordable, and can be built relatively quickly. But before you start digging, let's talk about planning.
The key to a successful pole barn project is planning for multiple use purposes. After all, why settle for just a workshop when you could have a workshop and a weekend getaway?
Step 1: Dream Big (and Realistic!)
Think about what you envision using your pole barn for. Do you need space for your woodworking projects, maybe a spot to park your vehicles, or perhaps a place for your chickens to roam free?
Maybe you want a guest room for visiting family, a cozy space to hang out with friends, or a private retreat to escape the hustle and bustle of everyday life. The possibilities are endless!
Step 2: Location, Location, Location
Where you build your pole barn matters. Consider the following:
Sunlight: Do you need lots of natural light for a workshop, or would you prefer shade for a relaxing hangout space?
Access: How easy is it to get to your desired location? Will you need to build a driveway, or is there already one in place?
Utilities: Can you easily connect to electricity, water, and internet? These might seem like obvious considerations, but they'll save you headaches down the road.
Zoning: Check your local building codes and zoning regulations to make sure your dream barn is actually possible.
Step 3: Size Matters
Once you know where you want to build, it's time to figure out how big your pole barn needs to be. This is where things get a little more detailed.
Don't be afraid to go big: Pole barns are typically more affordable than traditional buildings, so don't be afraid to think big. You might be surprised by how much space you actually need.
Think about the future: Even if you don't need all that space right now, it's better to build bigger than you think you'll need. You can always add more features later.
Consider layout: Think about how you want to divide up the space. Do you want a dedicated workshop area, a living space, a storage area, or a combination of all of these?
Step 4: Getting Down to Details
Now that you have a general idea of your layout, it's time to flesh out the details:
Doors and windows: Do you need large garage doors for parking, or would sliding doors be more practical? Consider natural light, ventilation, and security when deciding on windows.
Flooring: What kind of flooring will work best for your intended use? Concrete is durable and affordable, but hardwood or tile might be a better choice for a living space.
Insulation: Will you need insulation for heating and cooling purposes? Proper insulation can significantly improve comfort and energy efficiency.
Finishing touches: Think about lighting, paint, and any additional fixtures that will enhance your pole barn's functionality and style.
Step 5: DIY vs. Hiring Help
Building a pole barn is a great DIY project, but be honest with yourself about your skills and time commitment.
DIY: If you're handy and have the time, building your pole barn yourself can be a rewarding and cost-effective experience.
Hiring help: If you're not comfortable with the construction process, or if you simply don't have the time, there are plenty of contractors who specialize in pole barn construction.
Step 6: Embrace the Flexibility
One of the biggest advantages of a pole barn is its flexibility. You can easily adapt the space to your changing needs.
Remodeling: As your needs change, you can easily remodel and update your pole barn.
Adding features: You can add new doors, windows, or even a loft to create extra space.
Moving it: If you ever need to move your pole barn, it's relatively easy to dismantle and relocate.
Ready to Get Started?
Planning a pole barn project might seem daunting, but it's a rewarding experience. With careful planning and attention to detail, you can create a space that truly meets your needs and reflects your personal style.
Remember, it's your project, so embrace the possibilities and let your imagination run wild! From a cozy getaway to a multi-functional workspace, your pole barn can become the ultimate expression of your dreams.
How to Design a Pole Barn for Maximum Storage Efficiency
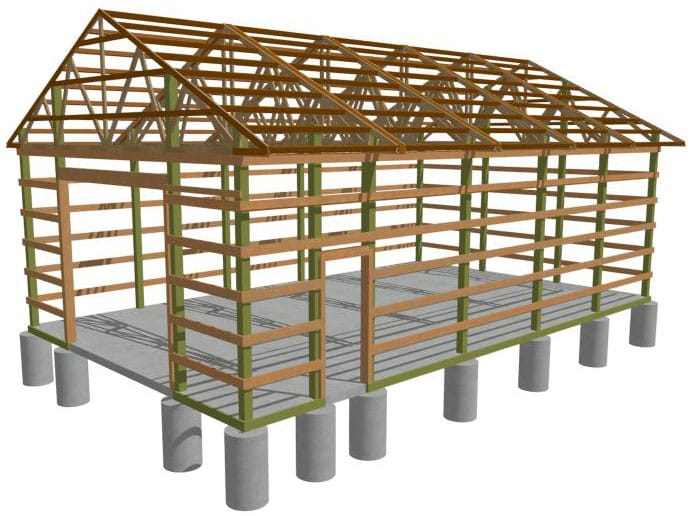
So, you're thinking of building a pole barn. Good choice! They're versatile, affordable, and perfect for tackling all your storage needs. But before you start digging holes and ordering lumber, let's talk about maximizing that storage potential. You want a barn that's not just big, but smart.
Think of it this way: your pole barn is like a blank canvas. It's up to you to paint it with efficiency and functionality. Let's explore how to make the most of every square inch, keeping your stuff organized and easily accessible.
First, Let's Talk About Size:
It's tempting to go big, but don't get carried away! Measure your belongings and plan for future storage needs. A 24x30 pole barn might seem massive, but you'll be surprised how quickly that space fills up. Consider these questions:
What are you storing? Are you housing vehicles, machinery, seasonal decorations, or a combination of everything?
How much growth do you anticipate? Will you be adding more to your collection over the next few years?
What's your budget? Building bigger means more materials and labor, so be realistic about your financial limitations.
Location, Location, Location:
While pole barns are versatile, think about how their location impacts your storage needs.
Sunlight: Do you want natural light for easier viewing and less reliance on electricity? If so, think about the orientation of your barn for maximum sun exposure.
Accessibility: Is your barn easily accessible for loading and unloading vehicles? Will it be easy to navigate large equipment inside?
Drainage: Make sure your barn is built on level ground with proper drainage to prevent water damage and ensure stability.
The Heart of the Matter: Storage Solutions
Now for the fun part â" designing the layout! Here's where you can get creative:
Shelving: Invest in sturdy shelving units that maximize vertical space. Use adjustable shelves to accommodate different sized items. You can even build your own using lumber and brackets for a budget-friendly solution.
Bins: Bins are a storage superhero! Label them clearly and categorize your belongings. Invest in stackable bins for maximum space efficiency.
Cabinets: For valuable tools and small parts, dedicated cabinets are a must. They keep things neat and organized, and offer added security.
Overhead Storage: Don't forget to utilize that space above your head! Install a sturdy overhead storage system for items you access less frequently.
Workbenches: A well-lit workbench is a must for any workshop or storage area. Choose a design that incorporates drawers or cabinets for added storage.
Pegboard: Pegboards are a great way to store tools and keep them easily accessible. They're affordable, customizable, and can be used for a variety of items.
Maximize Your Space:
Think outside the box for unique storage solutions. Here are some ideas:
Use the Walls: Hang bikes, ladders, or even gardening tools on the walls using hooks, racks, and wall-mounted shelves.
Go Vertical: Instead of having rows of boxes on the floor, utilize vertical storage solutions like towers or shelves.
Create Dividers: Separate your barn into designated areas using storage dividers. This makes it easy to find what you need and visually organize your space.
Light It Up:
Proper lighting is essential for a safe and functional workspace.
Natural Light: Utilize windows for natural light during the day.
Artificial Light: Install ample LED lighting for nighttime use. Choose bulbs with a high lumen output for maximum brightness.
The Finishing Touches:
Flooring: Choose durable flooring options like concrete or epoxy-coated floors that are easy to clean and resistant to stains.
Ventilation: Ensure proper ventilation to prevent moisture buildup and keep your storage area fresh.
Fire Safety: Install fire extinguishers and smoke detectors for added safety.
A Little Extra:
Label Everything: Clear and consistent labeling makes it easy to find what you need and keeps your storage organized.
Regularly Purge: Don't let clutter accumulate. Regularly purge your storage space to keep things organized and efficient.
Building Your Storage Sanctuary
Creating a storage sanctuary takes planning, but the rewards are worth it. By incorporating these tips and making thoughtful choices, you'll end up with a pole barn that's not just spacious, but a haven of organization and functionality.
Happy storing!
Sunday, November 10, 2024
How to build a 10x12 garden shed that maximizes space

Alright, you're ready to tackle a garden shed project, huh? A 10x12 shed â" that's a great size for a whole bunch of stuff. But you want to maximize space? You want to get the most out of every square inch? You've come to the right place! I'm gonna walk you through the whole process, from the initial planning to the finishing touches.
First things first, planning:
Location, location, location: Pick a spot that's flat, well-drained, and accessible. You'll want to make sure your shed is close enough to your house for convenience, but far enough away that it doesn't block your view or create drainage issues.
Think about your needs: What will you store in your shed? Tools, lawn equipment, bikes, maybe a small workbench? Make a list and then sketch out a rough floor plan. This will help you decide on the size and placement of windows, doors, and shelves.
Local building codes: Don't forget about those pesky regulations! Check with your local building department to see what permits and codes you need to follow. This might affect things like foundation type and wall materials.
Foundation: You've got options here: concrete, gravel, or even treated wood. Concrete is the strongest, gravel is budget-friendly, and wood is a good middle ground. Consider your budget and the weight of what you'll be storing.
Materials: Do you want to go with wood, metal, or something else? Wood is classic and versatile, but it requires more maintenance. Metal is durable and low-maintenance, but it can be more expensive.
Building the shed:
Framing: Get yourself some pressure-treated lumber â" it'll resist rot and bugs. You'll need to build a sturdy frame for your walls and roof. Use a level and measuring tape to make sure everything is square and plumb.
Sheathing: This is the layer that goes on top of the framing. You can use plywood, OSB, or even tongue-and-groove boards. Make sure it's securely fastened to the framing.
Roof: There are two main types of roofs: gable and shed. Gable roofs are more traditional and have a steeper pitch, which is good for shedding snow and rain. Shed roofs are simpler and less expensive. Choose the one that fits your style and climate.
Siding: This is what you'll see on the outside of your shed. Choose a material that's durable, attractive, and suits your budget. Vinyl siding is low-maintenance and comes in a variety of colors. Wood siding is classic, but requires more care.
Windows and doors: Place them strategically to maximize light and airflow. Think about your needs and how you'll be using the shed. For example, you might want a large door if you're storing a riding mower or a large workbench. Consider a window in the back if you want to work in the shed but still have natural light.
Maximizing Space:
Vertical Storage: Don't just think horizontally! Hang things on the walls, install shelves, and use vertical storage systems. You can maximize your storage space by using every inch from floor to ceiling.
Shelving: Build shelves from scratch or buy pre-made ones. Make sure they're strong enough to support the weight of your items. Consider adding a few deeper shelves for larger items.
Hanging solutions: Hang tools on pegboards, use hooks for rakes and brooms, and install hanging organizers for gardening supplies.
Mobile Storage: Utilize rolling carts or drawer units for easy access to tools and supplies. You can easily move them around as needed.
Utilize corners: Don't let those awkward corners go to waste! Use corner shelves, tiered organizers, or rotating shelves to make the most of those spaces.
Utilize the roof: If you have a gable roof, consider adding a loft for extra storage. Just make sure it's safe and accessible.
Lighting: Install good lighting so you can see what you're doing. Consider LED lights for energy efficiency.
Ventilation: Add vents or a small window for airflow to prevent mold and mildew.
Keep it organized: Label shelves, containers, and tools. This will help you find things quickly and easily.
Finishing touches:
Paint or stain: Give your shed a fresh coat of paint or stain to protect it from the elements and make it look great.
Landscaping: Add some landscaping around your shed to create a welcoming space.
Add personal touches: Hang a sign, put up a birdhouse, or plant a few flowers. Make it your own!
Remember:
Safety first! Always follow safety precautions when working with power tools and ladders.
Take your time! There's no need to rush. Enjoy the process and take pride in your work.
Ask for help if you need it! There are plenty of resources available online and at your local hardware store.
You've got this! Building a shed might seem daunting, but it's a rewarding project. With a little planning and effort, you can build a beautiful and functional shed that will serve you for years to come. And trust me, you'll be amazed at how much storage space you can create in a 10x12 footprint!
Saturday, November 9, 2024
Budget-friendly 8x10 shed design tips for diy builders

Hey there, fellow DIYer! So, you're thinking about building a shed, huh? An 8x10 is a great size, perfect for storing tools, bikes, garden supplies, or even a little workshop. But let's be real, sometimes the cost of building a shed can be a bit daunting. Don't worry, you don't need to break the bank to build your dream shed. We're gonna dive into some budget-friendly strategies and design tips to make your shed a reality without sacrificing quality.
1. The Foundation - Keep it Simple (and Cheap!)
Your foundation is the base of your shed, so it's important to get it right. But you don't need to go overboard. A simple concrete slab is a great option, especially if you're dealing with a relatively flat area. However, if your soil is uneven, a gravel pad might be a more practical and cost-effective choice. Just make sure to get a good layer of compacted gravel for stability.
2. Framing - Choose Your Material Wisely
For the framing, you have options. Treated lumber is a good choice because it's resistant to rot and insects, but it can be more expensive. Pressure-treated lumber is even better but comes with a higher price tag. If you're on a tight budget, consider using standard framing lumber and adding a few extra layers of paint or sealant for extra protection.
3. Roof - Don't Overcomplicate it
A simple gable roof is the most economical option. It's easy to build and requires less material than a more complex roof design. Consider using plywood for the roof sheathing â" it's affordable and strong. If you're looking to save even more, you can use a roll of asphalt roofing shingles for the roof.
4. Walls - Think Thin, but Strong
You can save on materials by using thinner walls for your shed. Consider using 1/2-inch plywood or OSB for the wall sheathing. It's strong enough for an 8x10 shed and will save you money compared to thicker options.
5. Siding - Go for the Budget-Friendly Options
Vinyl siding is a classic and durable choice for sheds. However, it can be a bit pricey. Consider using wood siding â" you can get it in various styles and it's generally more affordable than vinyl. Or, if you're feeling creative, try using corrugated metal siding, a budget-friendly and modern-looking option.
6. Windows and Doors - Keep it Minimalistic
While windows can add light and ventilation to your shed, they also add cost. A single, small window can be enough for most sheds. Similarly, a standard single door is usually sufficient for an 8x10 shed, saving you money on hardware and materials.
7. Roofing - Keep it Simple and Durable
Asphalt shingles are a budget-friendly option for your roof. They're easy to install and provide good protection from the elements. If you want something a bit more stylish, you could consider using metal roofing, which is also relatively affordable and offers excellent durability.
8. Flooring - Choose the Right Material
For your shed floor, plywood is a classic and affordable option. Make sure to use a moisture-resistant plywood for a long-lasting floor. Alternatively, you could use concrete for a more durable floor, especially if you plan to use the shed for heavier tasks or storage.
9. Paint - Choose a Durable, Affordable Option
Paint is a crucial part of your shed's exterior, protecting it from the elements and giving it a finished look. Choose a durable and affordable paint, like a latex acrylic paint. You can get these in a variety of colors to match your style and preferences.
10. The Finishing Touches - Add Value Without Breaking the Bank
Adding some finishing touches can really elevate your shed's look. A simple trim around the windows and doors adds a touch of elegance without breaking the bank. You can also consider adding some landscaping around the shed, like a small flower bed or a few shrubs, for a more finished and inviting look.
Building Your Shed: A Step-by-Step Guide
Now that you have some budget-friendly design tips, let's dive into the actual building process! Building a shed is a rewarding project, and with a little patience and elbow grease, you can do it yourself.
1. Planning and Design:
Measure your site and decide on the exact dimensions of your shed.
Draw up a plan to scale, including all the details like the roof pitch, window and door placement, and any other features you want.
Make a materials list. It's a good idea to add about 10% extra for potential mistakes or unexpected needs.
Consider the local building codes and permits. Some communities may require a permit for building a shed.
2. Foundation:
Prepare the ground by leveling the area and removing any vegetation.
Pour a concrete slab or create a gravel pad, depending on your budget and soil conditions.
Make sure the foundation is perfectly level to ensure a stable structure.
3. Framing:
Cut and assemble the framing using the measurements from your plan.
Use a level and plumb bob to ensure the framing is straight and true.
Attach the framing to the foundation using appropriate fasteners.
4. Sheathing and Roofing:
Attach plywood or OSB sheathing to the walls and roof using nails or screws.
Install the roof rafters and sheathing.
Add a layer of roofing felt to create a water-resistant barrier.
Install the roofing material, shingles, metal, or whatever you choose.
5. Siding and Trim:
Install the siding of your choice, making sure to follow the manufacturer's instructions.
Add trim around windows, doors, and the roof edge for a finished look.
6. Windows and Doors:
Cut out the openings for the windows and doors, making sure they're the correct size.
Install the windows and doors following the manufacturer's instructions.
7. Flooring:
Lay down the plywood or concrete floor, making sure it's level and securely fastened.
8. Painting and Finishing:
Paint the exterior of your shed to protect it and give it a finished look.
Consider adding landscaping around the shed to enhance its aesthetics.
Conclusion: Building Your Dream Shed on a Budget
Building your own shed can be a rewarding and fun project. By following these budget-friendly tips and using these resources, you can create a beautiful and functional shed without breaking the bank. Remember, it's about finding the right balance between cost and quality. With a little planning and creativity, you can build a shed that meets your needs and fits your budget. Happy building!
Friday, November 8, 2024
Step-by-step 8x12 shed plans for the budget-conscious builder
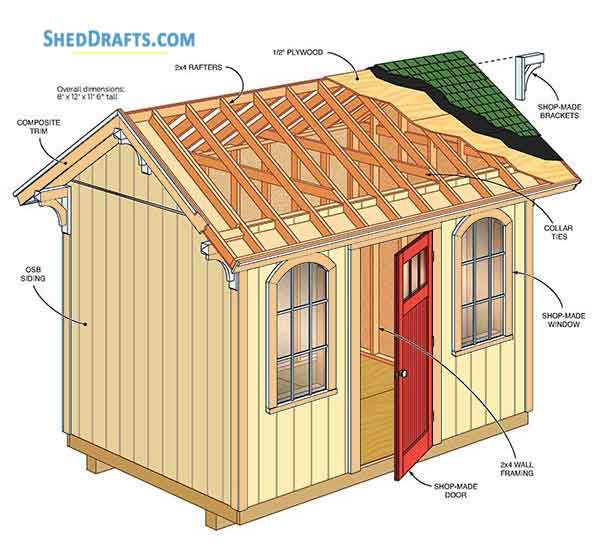
Alright, so you're thinking about building a shed. You want something practical, something that'll hold all your stuff, but you don't want to break the bank. I get it. That's why I'm here to walk you through building an 8x12 shed, the budget-friendly way.
Now, I'm not talking about cutting corners. I'm talking about smart choices, DIY smarts, and maybe even a few resourceful tricks. We're gonna build a solid, sturdy shed, without sacrificing quality or your wallet.
Step One: The Foundation - It's the Key to Everything
Think of your shed's foundation like the bedrock of your project. Get it wrong, and everything else suffers.
Concrete: This is the most solid foundation, and it's not as scary as you think. You can pour a simple, rectangular slab. Just make sure it's level and has a slight slope for drainage. You can DIY this with pre-mixed concrete or hire a contractor to help.
Pressure-Treated Skirts: This is the budget-friendly option, especially for folks who aren't into concrete. Just create a frame of pressure-treated lumber and screw it into the ground. Make sure the lumber is at least 6 inches deep and you've got good drainage.
Block Foundation: Similar to the pressure-treated skirt, you can build a foundation using concrete blocks. This offers a bit more height and is a solid option if you're dealing with uneven ground.
Step Two: Framing - Building the Skeleton
Alright, time to get your hands dirty! We're gonna start with the framing for the shed.
Lumber: Choose pressure-treated lumber for the bottom plates and anything that will touch the ground. For the rest of the frame, use standard dimensional lumber (2x4s and 2x6s).
Floor Joists: We're gonna build a strong, sturdy floor. Start by attaching 2x6 floor joists to the bottom plates, spaced 16 inches apart. Make sure to use joist hangers for a secure connection.
Wall Framing: Here's where you'll need to be a bit precise. You're building the walls, so use a level and plumb bob to make sure everything is square and straight. Use 2x4s for the wall studs, spaced 16 inches apart.
Roof Framing: This is where things get a bit more interesting. The roof is going to be supported by rafters, which need to be cut to the correct angle. You can use a rafter calculator or find diagrams online to help you determine the angle.
Step Three: Sheathing - Laying the Base
Now we're gonna start building the walls and the roof.
Plywood Sheathing: This is the base layer of the shed. Use plywood to cover the walls and roof. This will provide structure and a solid surface to attach the siding and roofing.
Wall Sheathing: Use plywood or OSB to sheathe the walls. Make sure you attach it securely with screws or nails.
Roof Sheathing: For the roof sheathing, you can choose plywood or OSB. Make sure it's installed with a slight overhang on the edges to protect the walls from rain.
Step Four: Roofing - Keeping the Weather Out
Now it's time to add the roofing.
Underlayment: Before you start attaching the shingles, install roofing felt or underlayment. This will help protect the roof from leaks and weather damage.
Shingles: Choose the type of shingles you prefer â" asphalt shingles are a popular and affordable option. Install them according to the manufacturer's instructions, paying attention to overlap and nailing patterns.
Step Five: Siding - Giving Your Shed Some Style
Time to give your shed some personality!
Siding Options: You've got tons of options for siding: vinyl, fiber cement, wood. Choose what works best for your budget and style.
Installation: Install the siding according to the manufacturer's instructions. Make sure it's properly overlapped and secured to the sheathing.
Step Six: Windows and Doors - Let the Light In!
Time to add those finishing touches!
Windows: Choose windows that fit your needs and budget. Don't forget to consider the size and location of the windows.
Doors: Consider a solid core door for security and durability. Make sure it's properly fitted and secured to the frame.
Step Seven: Finishing Touches - Making Your Shed Shine
Almost there! We just need to add a few finishing touches.
Paint: Give your shed a fresh coat of paint to protect the wood and add some color.
Trim: Add trim around the windows, doors, and corners to give the shed a polished look.
Gutters: If you're in an area with a lot of rain, install gutters to direct water away from the shed.
Step Eight: The Finishing Touches - Making Your Shed a Home
You've built a shed! Time to make it a home for all your things.
Shelving: Add shelving inside the shed for storage. You can use ready-made shelving or build your own.
Lighting: Install lights inside the shed to make it easy to see what you're doing.
Workbenches: If you plan on using the shed for DIY projects, add a sturdy workbench for working on projects.
The Budget-Conscious Approach
Shop Around: Compare prices for lumber, siding, roofing, and other materials. Don't be afraid to negotiate and ask for discounts.
Reclaimed Materials: Look for recycled or reclaimed materials. You can often find good deals on lumber, windows, and doors.
DIY: As much as you can, do the work yourself. This can save you a significant amount of money.
Ask for Help: Don't be afraid to ask for help from friends or family. A helping hand can make the project go faster and more efficiently.
Building a shed is a rewarding project, and it doesn't have to break the bank. By using these tips and planning carefully, you can build a sturdy, functional shed that will last for years to come.
Thursday, November 7, 2024
Diy garden shed plans for efficient and organized storage

So, you're finally taking the plunge and building your own garden shed. You envision a haven of organization, a space where every tool, every plant pot, every pair of gardening gloves has its place. It's going to be a masterpiece of efficiency and a joy to use.
Well, buckle up, friend, because we're about to dive into the world of DIY garden shed plans. We're going to walk through everything from the initial design to the final touches, ensuring your shed is not just functional but also a testament to your organizational skills.
Step 1: Designing Your Dream Space
Before you start hammering nails, it's crucial to have a clear vision of your shed's purpose. What will you store in it? Gardening tools, bikes, lawnmower, paint, potting mix? Take a good look at your current storage situation and make a list of everything you'll need space for.
Now, think about your space:
Size: How much stuff are you dealing with? A small shed might be enough for a few tools and some potting mix, while a larger one might be needed for bikes, lawnmowers, and bulky outdoor furniture.
Location: Consider the shed's location. Will it be easy to access? Is it close to power sources, if needed?
Style: Want something classic and charming? Modern and sleek? There's a shed style to suit every taste.
Pro tip: Think about the shed's roof pitch. A steeper pitch will shed rain and snow more effectively.
Step 2: Choosing Your Materials
Once you've got the design down, it's time to choose the materials. Here's a quick rundown of the most common options:
Wood: A classic choice for sheds, wood is durable, easy to work with, and adds a touch of charm. However, it needs regular maintenance to prevent rot and insect damage.
Metal: Metal sheds are durable, require little maintenance, and are resistant to moisture and pests. They can, however, be prone to rust and dents.
Plastic: Plastic sheds are lightweight, affordable, and low maintenance. They can also be good insulators. However, they aren't as sturdy as wood or metal and might not be ideal for extreme weather conditions.
Tip: Choose materials that match the style of your home and your budget.
Step 3: Planning Your Storage
Here's where the magic of organization truly begins. This is about optimizing every square inch of your shed.
Shelving: Shelving is essential for maximizing vertical space. Build sturdy shelves from wood or metal, and consider adding adjustable brackets for flexibility.
Hooks and Pegs: These are perfect for hanging tools, rakes, shovels, and other items that can be hung up. Invest in heavy-duty hooks and pegs to avoid accidental slippage.
Pegboards: Pegboards offer endless possibilities for organization. Use them to store tools, gardening accessories, and even small items like plant markers.
Bins and Containers: These are ideal for storing smaller items like seeds, fertilizers, and gardening supplies. Label them clearly for easy identification.
Tool Boxes: A dedicated tool box is a must-have for keeping your tools organized and protected from the elements.
Step 4: Getting Your Hands Dirty
Now it's time to get your hands dirty and start building!
Foundation: A solid foundation is crucial for a stable shed. You can build a simple foundation of concrete blocks, pavers, or a concrete slab.
Framing: Once your foundation is in place, you can start framing the walls and roof. Use pressure-treated lumber for the base and framing to resist moisture damage.
Siding: Choose the siding that best suits your design and budget. Wood, metal, and plastic siding are all viable options.
Roofing: A sturdy roof is essential to protect your belongings. Asphalt shingles are a common and affordable option, while metal roofing is more durable and longer-lasting.
Doors and Windows: Select doors and windows that match your shed's style and provide adequate ventilation.
Pro Tip: Don't forget to include proper ventilation to prevent moisture buildup.
Step 5: The Finishing Touches
Now that the structure is up, it's time to personalize your space and add those finishing touches:
Painting: A fresh coat of paint will not only make your shed look great but also protect it from the elements. Choose a durable paint that's suitable for outdoor use.
Lighting: Install adequate lighting inside the shed for visibility when working in the evening or on gloomy days.
Electrical Outlets: Consider adding electrical outlets for powering tools or charging devices.
Step 6: Enjoying Your Organized Haven
Congratulations! You've built your own dream garden shed. Now, take a step back and admire your creation. You've created a space that is both functional and organized. It's a place where you can enjoy your gardening hobbies and keep your tools and supplies safe and sound.
Bonus Tips:
Build in some extra storage: You never know when you might need more space. Consider adding an extra shelf or two, or even a small loft for seasonal items.
Invest in high-quality tools: Good tools will last longer and make gardening more enjoyable.
Keep your shed clean and organized: Make a habit of putting things away after use. This will keep your shed tidy and make it easier to find what you need.
Building your own garden shed is a rewarding experience that will bring you years of enjoyment. It's a project that allows you to express your creativity and create a space that's perfectly tailored to your needs.
How to design a 8x12 shed on a budget and make it last
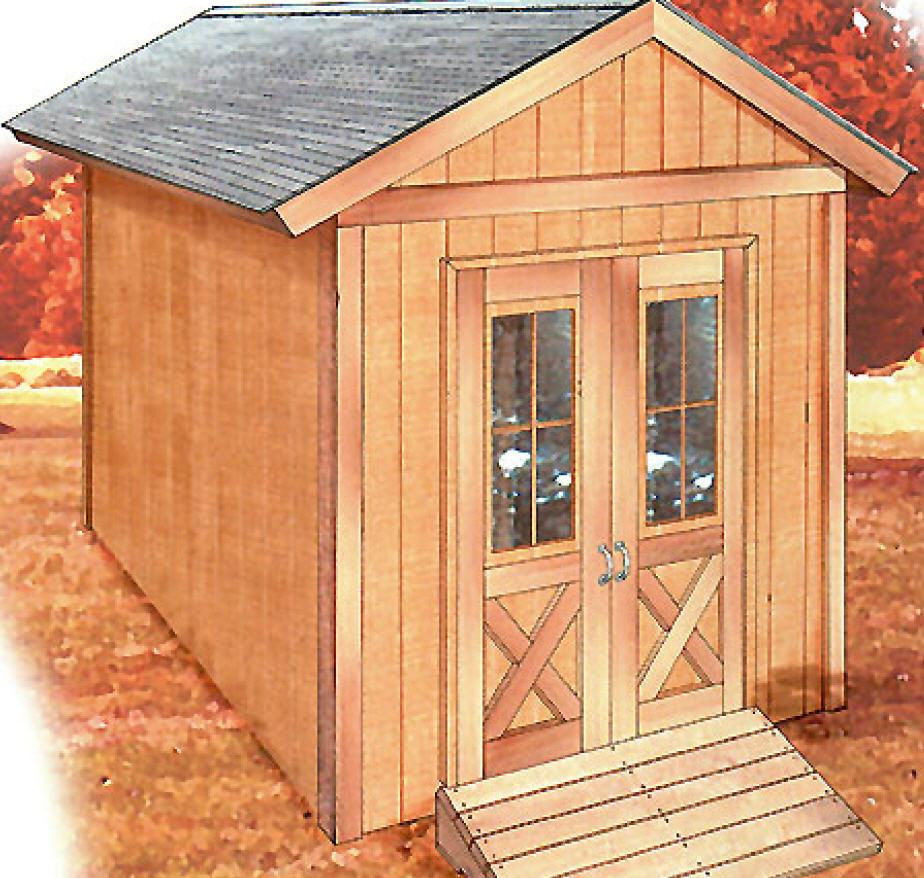
Alright, so you're thinking about building an 8x12 shed, huh? Smart move! Those are super versatile and great for storage, a workshop, or even a little hangout space. And you want to do it on a budget? I get it, building ain't cheap. But don't worry, with some smart choices, you can have a solid shed that'll last for years. Let's break it down, shall we?
First, the Foundation:
This is the base of your shed, so it needs to be strong! You have a few options here, and the "best" one depends on your soil type and what your local building codes say.
Concrete Slab: This is the most durable and long-lasting option. You'll need to pour a concrete slab, but you can do it yourself with some help (or hire a contractor). This will cost more upfront, but it'll save you headaches in the long run.
Concrete Blocks: These are a good option for a simpler foundation. You can lay them in a pattern and build up the walls. It's cheaper than a slab, but may not be as sturdy, depending on your soil.
Pressure-Treated Wood Skirts: If your soil drains well, this is a budget-friendly choice. You'll use pressure-treated lumber to create a frame around the perimeter of the shed. Make sure to use heavy-duty lumber and secure it well to the ground. You'll want to add a layer of gravel under the floor for drainage.
The Framing:
This is the bones of your shed. Again, you have choices to make here.
Lumber: The classic choice for framing is lumber, specifically 2x4s or 2x6s. You can buy these pre-cut or cut them yourself. Make sure to choose pressure-treated lumber for the bottom plates and any parts that will be in contact with the ground.
Steel: Steel framing is becoming more popular because it's durable and resistant to rot and pests. It can be a bit more expensive upfront, but you might save money in the long run. You'll need to be careful with the weight, though, and maybe get some help lifting those beams.
Walls & Roof:
Now we're getting to the fun part!
Sheathing: This is the layer that goes on the walls and roof to provide a solid base for siding and roofing. You can use plywood, OSB (oriented strand board), or even metal panels. Plywood is a little pricier but will provide a smoother surface for siding.
Siding: Think about the look you want! Vinyl siding is affordable and easy to maintain. Wood siding can be more expensive, but it's classic and beautiful. You could even go with metal siding for a modern look and some extra durability.
Roofing: Asphalt shingles are the most common choice, and they come in a wide range of colors and styles. Metal roofing is a bit more expensive, but it lasts longer and is more energy-efficient. If you're going for the rustic look, you could even consider shingles made from cedar or other wood.
The Details:
Windows and Doors: These can make your shed more inviting and provide natural light. You can go with standard windows and doors or get creative with something unique. Think about the size and placement of your windows to maximize natural light.
Insulation: If you plan on using your shed for a workshop or hangout space, consider adding insulation to keep it comfortable year-round. There are different types of insulation available, so choose what's best for your budget and needs. This will also help you save on heating and cooling costs.
Finishing Touches: Don't forget the finishing touches! Paint or stain the exterior to protect the wood and add color. Add a trim around the windows and doors for a polished look. And consider adding a porch, a ramp, or some landscaping to enhance the look of your shed.
The DIY vs. Contractor Dilemma:
This is where it gets tricky. Building a shed yourself can save you money, but it requires time and skills. If you're not comfortable with carpentry and construction, it's probably better to hire a contractor. They'll have the experience and equipment to build a high-quality shed that's up to code. But if you're up for the challenge, there are plenty of resources available to help you along the way. Check out books, websites, and YouTube videos to learn the basics of construction.
The Budget Breakdown:
Okay, let's talk about money. This is where things get a little more concrete (pun intended). Here's a general breakdown of what you can expect to spend on an 8x12 shed, but keep in mind these are estimates and your actual costs may vary depending on your location and choices:
Foundation: $300-$1500 (depending on the type)
Framing: $300-$800 (depending on the type and material)
Sheathing: $150-$300
Siding: $200-$800
Roofing: $200-$800
Windows and Doors: $100-$500
Insulation: $100-$300
Finishing Touches: $100-$300
Tips for Staying on Budget:
Shop Around: Compare prices from different lumberyards and home improvement stores.
Buy in Bulk: If you're comfortable buying in bulk, you can often get a discount.
Recycle and Repurpose: Use salvaged materials whenever possible to reduce costs.
Get Help: Don't be afraid to ask friends or family for help with the construction.
Don't Rush: Take your time and plan carefully to avoid costly mistakes.
Building Your Shed:
Okay, you've got your materials, you've got your plans, and you're ready to build! Here are some tips for a smooth and successful construction:
Start with the Foundation: Make sure your foundation is level and stable before you start building the walls.
Measure Twice, Cut Once: Accuracy is key! Measure carefully and double-check your measurements before you start cutting lumber.
Use the Right Tools: Invest in good quality tools for accurate cutting and assembly.
Take Breaks: Building a shed can be tiring! Don't try to do too much in one day. Take breaks and stay hydrated.
Have Fun: Building a shed is a great way to learn new skills and create something tangible. Enjoy the process and be proud of your accomplishment!
So there you have it! You now have a solid foundation for building your own 8x12 shed on a budget. With a little planning, effort, and maybe a few extra hands, you can create a versatile and long-lasting space for all your needs. Remember, this is just a guide, so feel free to adjust the plans and materials to suit your specific needs and budget. Good luck! And don't forget to share pictures when you're done!
8x10 shed plans with cost-cutting tips for diy builders
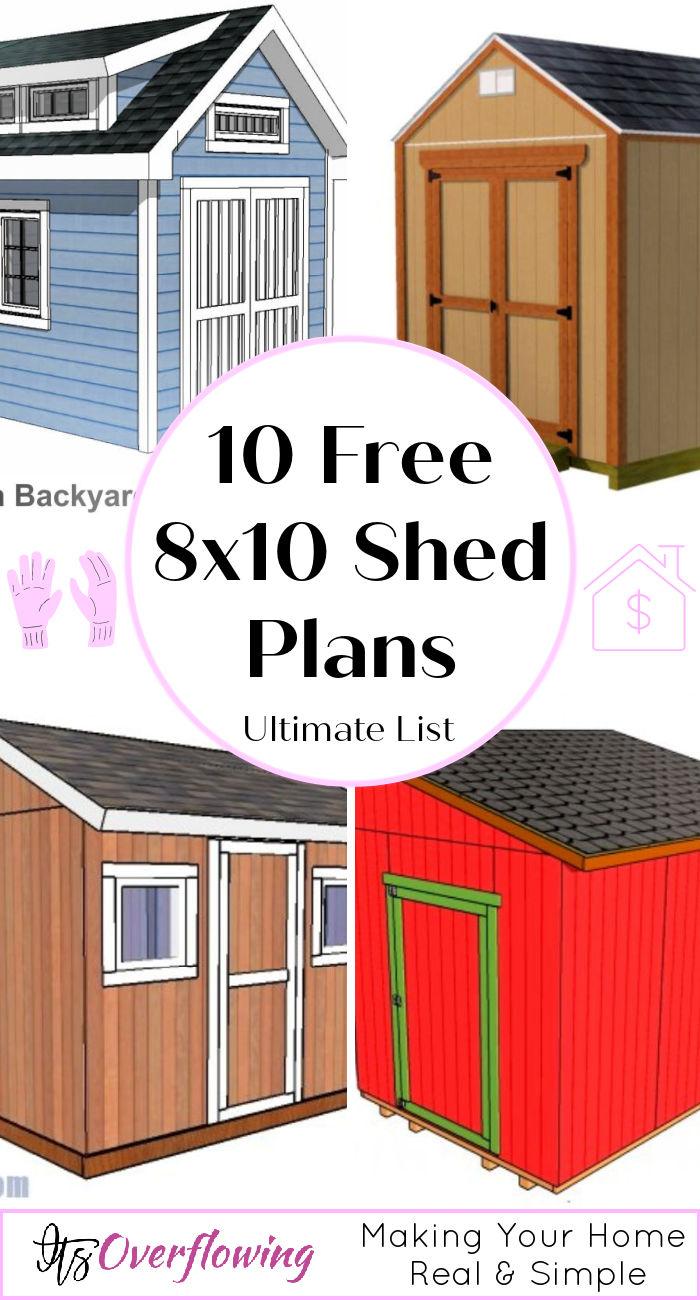
Alright, folks, youâre ready to tackle a DIY project thatâll give your backyard a serious upgrade: building your own 8x10 shed! You're looking for some extra storage space, a workshop, maybe even a little mini-getaway. Whatever your reason, Iâm here to help you build it without breaking the bank.
Before we dive into the nuts and bolts (pun intended!), letâs talk about the benefits of building your own shed:
Cost Savings: You'll save a ton compared to buying a pre-made shed. Itâs a serious investment, and you'll be surprised how much you can save by doing the work yourself.
Customization: You get to decide on the design, materials, and features that work best for you. No need to settle for something that doesnât quite fit your needs.
Sense of Accomplishment: Thereâs nothing quite like seeing a project you built with your own two hands. You'll feel a genuine sense of pride knowing you tackled it yourself.
Now, let's get into the nitty-gritty of building your 8x10 shed on a budget:
1. Planning is Key:
Sketch Your Design: Donât jump into buying materials without a clear plan. Take some time to sketch out your shedâs layout, considering doors, windows, and any extra features you want. Remember, you're building a 8x10, so you want to maximize your space.
Choose the Right Location: Picking the right spot for your shed is crucial. Consider factors like drainage, sunlight, and access for building materials. Make sure youâre not violating any local zoning regulations.
Building Permit Check: Before you start digging, check with your local authorities about permits. It might seem like a hassle, but itâs important to be on the right side of the law.
Get Your Materials List: Based on your design and plans, create a detailed list of materials. This will help you stay organized and avoid last-minute trips to the hardware store.
2. Materials: Choosing the Right Stuff for Your Budget:
Foundation: You can save money on a concrete slab by opting for a cheaper alternative like gravel pads, wooden piers, or cinder blocks. If you're going for a foundation, consider a basic slab â" you can always build a floor on top later.
Framing: Pressure-treated lumber is a great option for the foundation and lower walls. Itâs moisture-resistant and will last longer. For the rest of the framing, consider using standard lumber.
Siding: Opt for affordable siding like vinyl, fiber cement, or even corrugated metal. You might be able to find good deals on salvaged materials or leftover pieces from other projects.
Roofing: Shingles are a classic choice for roofs, but consider using metal roofing. Itâs durable, long-lasting, and can be easier to install.
Windows and Doors: Go for basic, functional windows and doors. You can find decent quality doors and windows at affordable prices, especially if you shop around.
3. Cost-Cutting Tips Every DIYer Can Use:
Shop Around: Don't just settle for the first price you see. Compare prices at different hardware stores, lumberyards, and online retailers. Youâll be surprised at how much you can save by finding the best deals.
Look for Sales: Keep an eye out for sales and clearance events. You can snag great deals on lumber, tools, and other materials. Those "oops" stacks at the hardware store are often a gold mine!
Reclaim Materials: Don't discount the value of repurposed materials. Check local salvage yards, demolition sites, or online marketplaces like Craigslist for salvaged lumber, windows, or doors. Youâd be surprised what treasures you can find.
Make Your Own: You can save money by cutting your own lumber or building certain components yourself. If you're a bit handy, you can even make your own doors or windows, saving even more.
Don't Skimp on Quality: While you're trying to save money, don't compromise on quality. It's better to spend a little more upfront on high-quality materials that will last longer. It's a much better investment.
Use Your Network: Reach out to friends and family who might have tools or equipment you can borrow. You can also ask around for recommendations on contractors or local businesses that offer affordable materials or services.
4. Construction: Time to Get Your Hands Dirty:
Laying the Foundation: Start by preparing the ground and laying your foundation. This is a critical step, so take your time and make sure itâs level.
Framing the Walls: Once the foundation is ready, start framing the walls. Use a level to ensure the walls are plumb and square. You can add insulation for extra warmth and soundproofing.
Roof Framing: Building the roof is a bit trickier, but it's manageable with some careful planning. Use a roof truss system or build your own rafters for support.
Siding and Roofing: After the framing is complete, you can install the siding and roofing. Again, take your time and make sure the work is done properly.
Doors and Windows: Install your doors and windows, ensuring they fit securely and are weather-resistant.
Finishing Touches: Once the shed is built, you can add finishing touches like painting, trim, and any extra features you want.
5. Tips for Success:
Be Patient: Building a shed is a process that takes time and patience. Don't rush it â" take your time to do the work right.
Read the Instructions: Before you start any task, read the instructions carefully. It will save you time and prevent mistakes.
Don't Be Afraid to Ask for Help: If you're not sure about something, don't be afraid to ask for help from a friend, family member, or experienced DIYer.
Have Fun: Building a shed should be enjoyable! So, relax, take breaks, and enjoy the process.
6. Safety First:
Wear Safety Gear: Always wear safety glasses, gloves, and sturdy footwear when working.
Use the Right Tools: Use tools properly and always follow the manufacturer's instructions.
Be Aware of Your Surroundings: Be mindful of your surroundings and keep the work area clean and tidy.
Work in a Safe Environment: Make sure you have adequate lighting and ventilation.
Building your own 8x10 shed can be a rewarding experience. You'll gain valuable skills, save money, and create a valuable addition to your backyard. Just remember, take your time, plan carefully, and don't be afraid to ask for help when needed. Happy building!
A beginnerâs guide to building a 10x12 garden shed

Hey there, fellow green thumbs and backyard enthusiasts! Ever dreamed of having a dedicated space for all your gardening tools, potting supplies, and maybe even a cozy spot to relax with a good book? Well, building your own 10x12 garden shed is a fantastic way to make that dream a reality! It's a project that might seem daunting at first, but trust me, it's totally achievable, even if you're a DIY newbie.
Think of it as a journey of discovery â" you'll be surprised at what you can accomplish with a little planning, some basic tools, and a whole lot of enthusiasm. Plus, building your own shed is incredibly rewarding! The satisfaction of seeing your creation come to life is priceless.
So, grab your favorite beverage, put on some tunes, and let's dive into the world of shed construction!
1. Planning is Key: Before You Even Grab a Hammer
Okay, before you get carried away with visions of your perfectly organized shed, let's talk about the practical stuff. Planning is crucial for a smooth and successful build.
Location, Location, Location: Where will your shed be built? Make sure you have enough space and access for building materials and your tools. Don't forget to check local building codes and zoning regulations!
Foundation: Concrete or Wood? This is a big decision. Concrete foundations are strong and long-lasting but more labor-intensive. Wooden foundations are easier to build but might require more maintenance.
Shed Design: Do you want a traditional shed with a pitched roof or a modern one with a flat roof? Think about the look and feel you're going for, and sketch out a basic design.
Materials: Decide on the type of wood you want to use â" pressure-treated lumber for the foundation and walls, plywood for the roof, and your choice of siding for the exterior.
Budget: Set a realistic budget and stick to it. Materials, tools, and even labor costs can add up quickly, so keep track of everything!
2. Gather Your Tools and Supplies
With the planning done, it's time to get your hands dirty! Here's a list of essential tools and supplies you'll need:
Tools:
Measuring tape
Level
Hammer
Circular saw
Drill
Screwdriver
Safety glasses
Work gloves
Materials:
Pressure-treated lumber for the foundation and walls
Plywood for the roof and floor
Siding of your choice (vinyl, wood, metal)
Roofing shingles
Doors and windows (optional)
Fasteners (screws, nails, etc.)
Wood glue
Paint or stain
3. Building the Foundation: The Base of Your Shed
Now, let's get started with the foundation! This is the most crucial part of the project.
Concrete Foundation: If you're going for concrete, hire a professional to pour it for you. You can also pour it yourself, but it requires a bit more skill and knowledge.
Wooden Foundation: For a wooden foundation, you'll build a simple frame using pressure-treated lumber. Make sure to use treated lumber to prevent rot and insect damage.
4. Framing the Walls: The Skeleton of Your Shed
Once the foundation is set, it's time to build the walls. This is a fun part!
Cut the lumber: Measure and cut the wall studs to the desired height.
Assemble the walls: Use wood glue and screws to attach the studs together. Make sure the walls are square and plumb (perfectly vertical).
Sheathing: Attach plywood sheathing to the outside of the walls for extra strength and support.
5. Building the Roof: Keeping Your Shed Dry
The roof is what protects your shed from the elements.
Rafters: Cut and assemble the rafters, which will support the roof. Make sure they are properly spaced and angled for the type of roof you've chosen.
Sheathing: Attach plywood sheathing to the rafters.
Roofing Underlayment: This helps prevent leaks and adds another layer of protection.
Shingles: Install the roofing shingles of your choice.
6. Finishing Touches: Adding Style and Function
You're almost there! Now, it's time to add the final touches.
Siding: Install the siding of your choice to the outside of the walls.
Doors and Windows: Install doors and windows to create access and let in natural light.
Flooring: Install flooring in the shed, making sure it's level and well-supported.
Painting or Staining: Give your shed a fresh coat of paint or stain to protect the wood and add some personality.
7. Finishing Touches: Making it Your Own
You've built a fantastic shed, but it's not quite complete until you personalize it!
Storage Solutions: Add shelves, pegboards, and drawers to create organized storage for your tools and supplies.
Electrical Work: If you want to add lights or outlets, hire an electrician to do the wiring safely.
Lighting: Install lights for nighttime visibility.
Ventilation: Add vents or windows to promote airflow and prevent moisture buildup.
8. Enjoying Your New Backyard Oasis
You did it! You've successfully built your own 10x12 garden shed. Now, sit back, admire your handiwork, and start enjoying your new backyard oasis.
Remember: Building a shed is a project that requires planning, patience, and a few basic tools. Don't be afraid to ask for help if you need it. And most importantly, have fun with it!
This is just a beginner's guide to building a 10x12 garden shed. There are many resources available online and at your local hardware store that can provide you with more detailed instructions and tips. Don't be afraid to experiment and customize your shed to make it your own. Happy building!
Tips for saving on materials with 8x10 shed plans
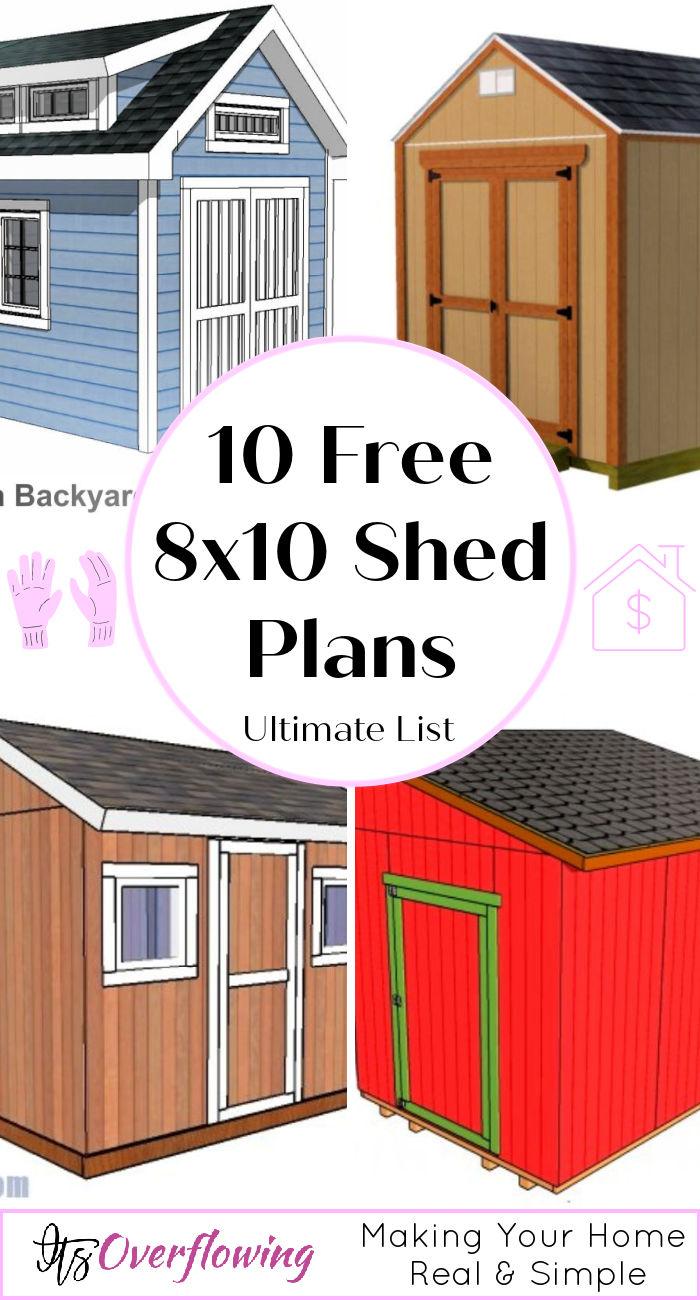
Okay, so you've got the itch. You're ready to build your own 8x10 shed, and that's awesome! A shed is a great way to add some much-needed storage space, a workshop, or even a tiny escape from the everyday grind. But let's be real, building anything can get expensive, and materials are a big part of that cost.
Don't worry, though, because I'm here to share some tips for saving on those materials without sacrificing quality. Let's dive in!
1. Get the Most Out of Your Lumber:
Think about your wood choices: You don't always need the most expensive lumber. Pressure-treated wood is fantastic for the foundation and floor, but for the walls and roof, standard framing lumber is generally enough. Consider using dimensional lumber like 2x4s and 2x6s for your framing, and plywood for sheathing.
Buy in bulk: This is a classic way to save. Contact your local lumber yard and see if they have discounts for bulk purchases. You might even be able to negotiate a better price if you're willing to buy a whole bundle of plywood or a full truckload of lumber.
Scrounge and salvage: Don't underestimate the power of free! Check Craigslist, Facebook Marketplace, or local salvage yards for gently used or leftover materials. You might find a great deal on framing lumber, plywood, or even roofing shingles! Just make sure they are in good shape and suitable for your project.
2. Don't Be Afraid to DIY:
Build your own doors and windows: This can be a great way to save money. You can often find pre-made doors and windows at affordable prices, but if you're handy with tools, consider building them yourself. There are tons of resources and tutorials online that can guide you through the process.
Make your own siding: Instead of using traditional siding, consider using cheaper alternatives like corrugated metal sheets or even reclaimed wood. It can give your shed a unique look and save you a lot of money.
Do your own roofing: This one might seem daunting, but it's not as hard as you think. You can find roofing shingles for a reasonable price, and there are lots of online resources and videos that will walk you through the process step-by-step.
3. Choose Affordable Alternatives:
Skip the fancy shingles: Traditional asphalt shingles are perfectly fine for a shed roof, and they're way more budget-friendly than fancy architectural shingles.
Go with a simple foundation: A concrete slab is the most durable, but it can also be expensive. A gravel pad or even a well-prepared wooden platform will work just fine for a shed.
Consider alternatives to paint: If you don't want to spend money on paint, you can stain or even seal your shed with a clear finish. This will protect the wood without hiding its natural beauty.
4. Shop Around and Compare Prices:
Don't settle for the first price you see: Check prices at multiple lumberyards, home improvement stores, and online retailers. You might be surprised at the differences in pricing.
Look for sales and clearance items: Lumberyards and home improvement stores often have sales on specific materials, and they might even have clearance items that you can score at a fraction of the original price.
Ask for discounts: If you're buying in bulk, don't be afraid to ask for a discount. Many lumberyards and retailers are willing to negotiate, especially if you're spending a significant amount of money.
5. The Little Things Add Up:
Invest in good tools: This might seem counterintuitive, but good tools will make your job easier and faster. And let's face it, you'll probably use those tools for other projects in the future.
Think about your fasteners: Use the right screws and nails for the job. Oversized fasteners are more expensive, and they can be a hassle to work with.
Don't forget the finishing touches: Consider what you need to complete your shed, like handles for your doors, hinges, and even light fixtures. These items can add up, so factor them into your budget from the start.
6. Get Creative and Have Fun:
Embrace the imperfections: No one expects your shed to be a perfect architectural masterpiece. Embrace the imperfections and remember that building something yourself is a great learning experience!
Be resourceful: Don't be afraid to get creative and use what you have on hand. You might be surprised at what you can find in your garage or shed.
Enjoy the process: Building a shed is a rewarding experience, and it's a great way to learn new skills. Don't get bogged down by the cost â" focus on the fun and satisfaction of creating something with your own two hands.
Remember, building a shed is a journey, not a race. Take your time, plan carefully, and you'll be amazed at what you can accomplish with a little bit of effort and a lot of creativity!
Bonus Tip: Recruit some help! Building a shed is definitely a two-person job, and having an extra set of hands can make the process faster and more enjoyable. Plus, you can share the cost of materials and tools, which is always a plus!
Building your own 8x10 shed can be a rewarding and cost-effective project. With a little planning and resourcefulness, you can build a beautiful and functional shed that you'll love for years to come. Happy building!